Wybór leczenia powierzchni jest problemem, przed którym stoi każdy projektant. Dostępnych jest wiele rodzajów opcji oczyszczania powierzchni, a projektant wysokiego szczebla powinien nie tylko rozważyć gospodarkę i praktyczność projektu, ale także zwracać uwagę na proces montażu, a nawet wymagania środowiskowe. Poniżej znajduje się krótkie wprowadzenie do niektórych powszechnie używanych powłok dla łączników opartych na powyższych zasadach, w odniesieniu do praktyków złącza.
1. Elektrogalwanizacja
Cynk jest najczęściej stosowaną powłoką dla komercyjnych elementów mocujących. Cena jest stosunkowo tania, a wygląd jest dobry. Wspólne kolory to czarny i wojskowy zielony. Jednak jego wydajność przeciw korozji jest średnia, a jego działanie antykorozyjne jest najniższym wśród warstw gatowania cynku (powłoki). Zasadniczo neutralny test rozpylania soli stali ocynkowanej odbywa się w ciągu 72 godzin, a specjalne środki uszczelniające są również stosowane w celu zapewnienia neutralnego testu rozpylania soli trwa przez ponad 200 godzin. Jednak cena jest droga, która jest 5-8 razy większa niż zwykła stal ocynkowana.
Proces elektrogalwanizacji jest podatny na kruchość wodoru, więc śruby powyżej klasy 10.9 na ogół nie są obróbane galwanizacją. Chociaż wodór można usunąć za pomocą piekarnika po poszycie, folia pasywacyjna zostanie uszkodzona w temperaturach powyżej 60 ℃, więc usuwanie wodoru należy przeprowadzić po galwanizacji i przed pasywacją. Ma to słabą operację i wysokie koszty przetwarzania. W rzeczywistości ogólne zakłady produkcyjne nie usuwają aktywnie wodoru, chyba że określone przez określonych klientów.
Spójność między momentem obrotowym a siłą przed dokręcaniem ocynkowanych elementów złącznych jest słaba i niestabilna i na ogół nie są używane do łączenia ważnych części. Aby poprawić spójność obciążenia wstępnego momentu obrotowego, można również zastosować metodę powlekania substancji smarujących po poszycie w celu poprawy i zwiększenia spójności obciążenia wstępnego momentu obrotowego.
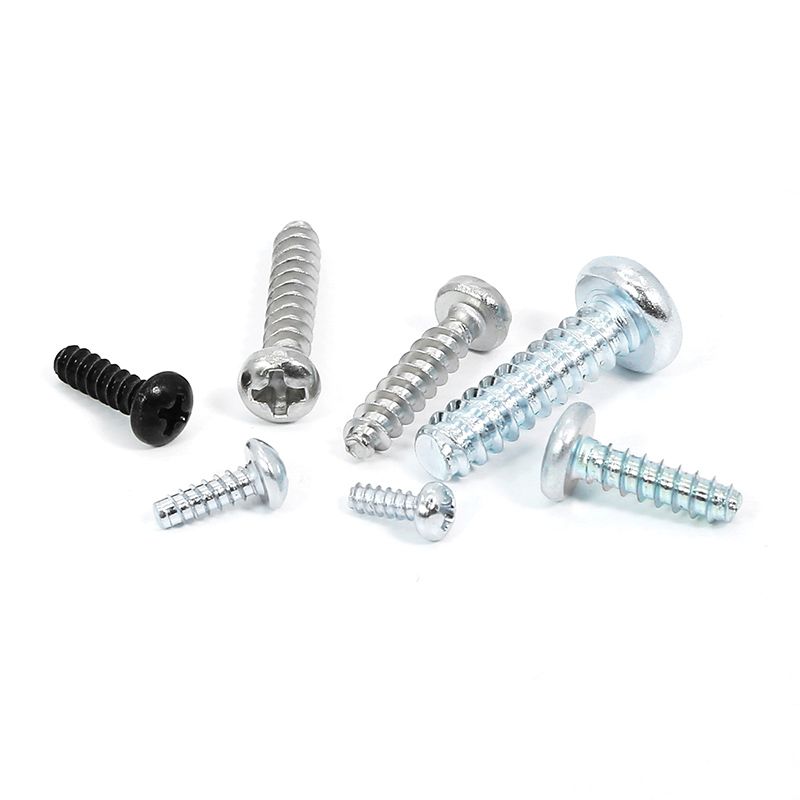
2. Fosforowanie
Podstawową zasadą jest to, że fosforowanie jest stosunkowo tańsze niż galwanizacja, ale jego odporność na korozję jest gorsza niż galwanizacja. Po fosformie należy zastosować olej, a jego odporność na korozję jest ściśle związana z wydajnością przyłożonego oleju. Na przykład po fosformie zastosowanie ogólnego oleju przeciw rdzewieniu i przeprowadzanie neutralnego testu sprayu solnego tylko przez 10-20 godzin. Zastosowanie wysokiej jakości oleju przeciw rdzewieniu może potrwać do 72-96 godzin. Ale jego cena wynosi 2-3 razy większa niż ogólny olej fosforowy.
Istnieją dwa powszechnie stosowane rodzaje fosforoty dla elementów złącznych, fosformy na bazie cynku i fosformy manganu. Fosforowanie na bazie cynku ma lepszą wydajność smarowania niż fosforowanie na bazie manganu, a fosforowanie na bazie manganu ma lepszą odporność na korozję i odporność na zużycie niż poszycie cynku. Może być stosowany w temperaturach od 225 do 400 stopni Fahrenheita (107-204 ℃). Szczególnie w przypadku połączenia niektórych ważnych elementów. Takie jak śruby i nakrętki prętów podłączania silnika, głowica cylindra, łożysko główne, śruby koła zamachowe, śruby koła i nakrętki itp.
Śruby o wysokiej wytrzymałości wykorzystują fosfor się, co może również uniknąć problemów związanych z kruchością wodoru. Dlatego śruby powyżej klasy 10.9 w polu przemysłowym zwykle stosują obróbkę powierzchni fosfortu.
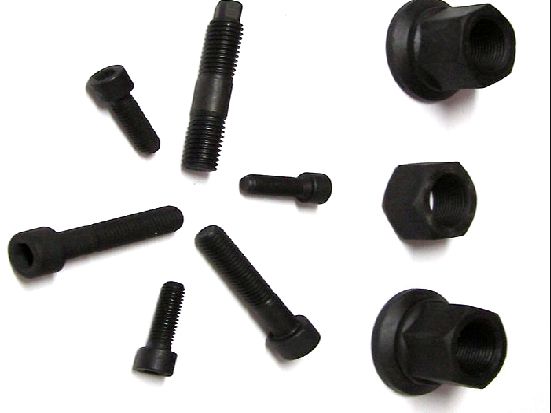
3. Utlenianie (zaczernienie)
Zaciemnianie+olejowanie jest popularną powłoką dla elementów złącznych przemysłowych, ponieważ jest najtańszy i wygląda dobrze przed zużyciem paliwa. Ze względu na jego zaczepienie prawie nie ma zdolności zapobiegania rdzeniom, więc szybko rdzewieje bez oleju. Nawet w obecności oleju test rozpylania soli może trwać tylko 3-5 godzin.
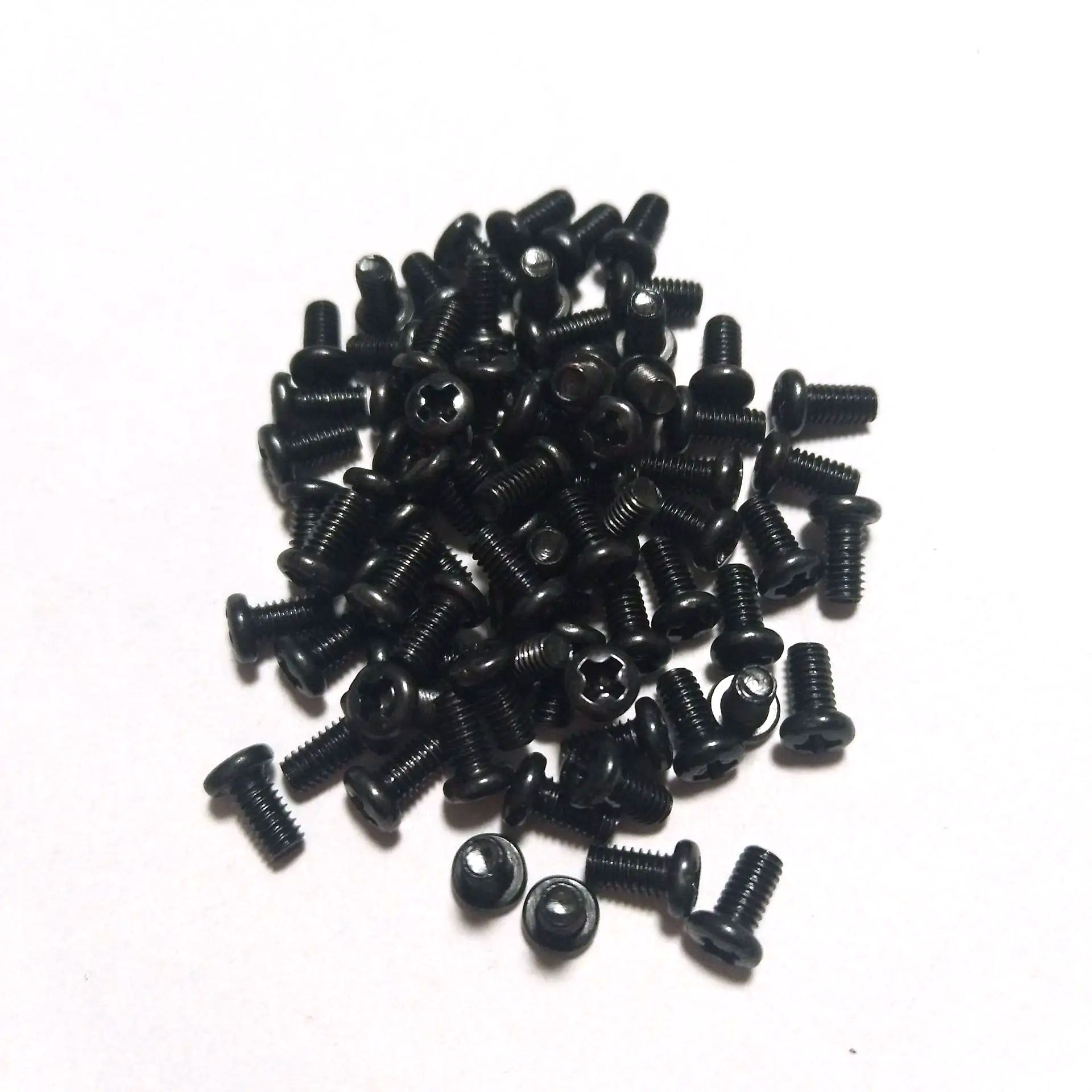
4. Partia galwaniczna
Posież kadmu ma doskonałą odporność na korozję, szczególnie w środowiskach morskich w porównaniu z innymi zabiegami powierzchniowymi. Koszt oczyszczania cieczy w procesie galwanicznego kadmu jest wysoka, a jego cena wynosi około 15-20 razy większa niż w przypadku galwanicznego cynku. Dlatego nie jest używany w branżach ogólnych, tylko dla określonych środowisk. Połączki używane do platform wiertniczych ropy i samolotów HNA.
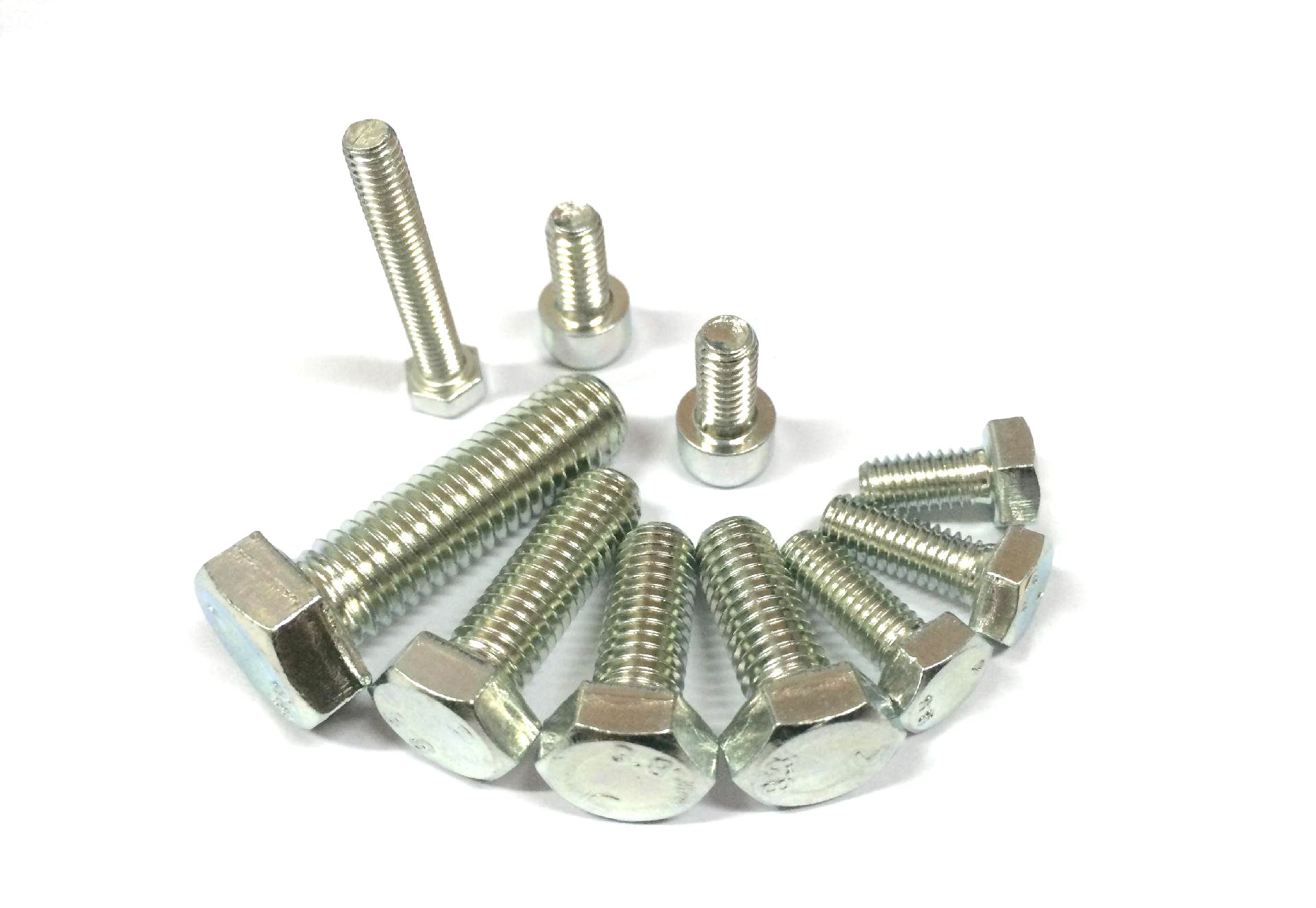
5. Splatanie chromu
Powłoka chromu jest bardzo stabilna w atmosferze, nie jest łatwa do zmiany koloru i utraty połysku, ma wysoką twardość i dobrą odporność na zużycie. Zastosowanie poszycia chromu na elementach złącznych jest zwykle stosowane do celów dekoracyjnych. Jest rzadko stosowany w polach przemysłowych o wysokich wymaganiach dotyczących odporności na korozję, ponieważ dobre chromowe elementy mocowane są równie drogie jak stal nierdzewna. Tylko wtedy, gdy wytrzymałość ze stali nierdzewnej jest niewystarczająca, zamiast tego stosuje się chromowane podłączniki.
Aby zapobiec korozji, miedź i nikiel należy najpierw wysiać przed chromowaniem. Powłoka chromowa może wytrzymać wysokie temperatury 1200 stopni Fahrenheita (650 ℃). Istnieje jednak problem kruchości wodoru, podobnie jak elektrogalwanizacja.
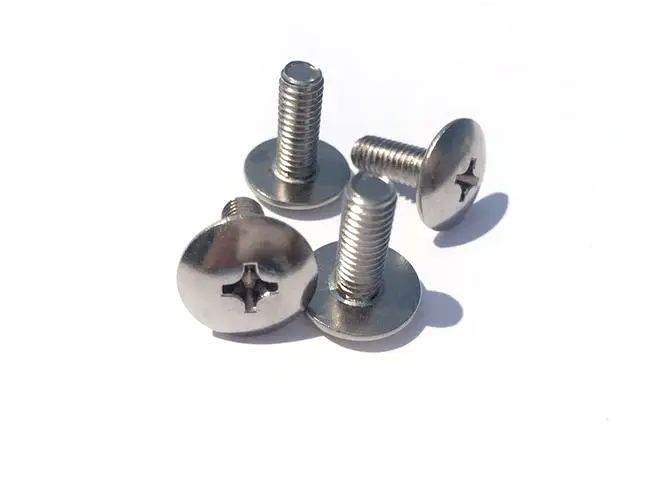
6. Nikiel Splat
Stosowane głównie w obszarach wymagających zarówno antykorozji, jak i dobrej przewodnictwa. Na przykład wychodzące terminale akumulatorów pojazdów.
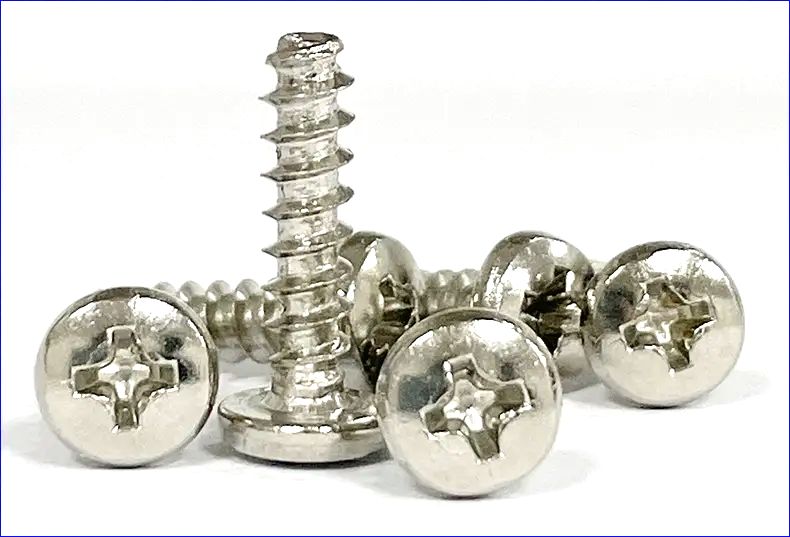
7. Galwanizacja na gorąco
Galwanizacja gorącego zanurzenia to termiczna powłoka dyfuzyjna cynku ogrzewanego do cieczy. Grubość powłoki wynosi od 15 do 100 μm. I nie jest łatwy do kontrolowania, ale ma dobrą odporność na korozję i jest często używany w inżynierii. Podczas procesu ocynkowania gorącego zanurzenia występuje poważne zanieczyszczenie, w tym odpady cynku i pary cynkowe.
Z powodu grubej powłoki spowodowało to trudności w wkręceniu gwintów wewnętrznych i zewnętrznych w elementach złącznych. Ze względu na temperaturę przetwarzania galwanizacji zanurzeniowego nie można go stosować w przypadku elementów łącznikowych powyżej klasy 10.9 (340 ~ 500 ℃).
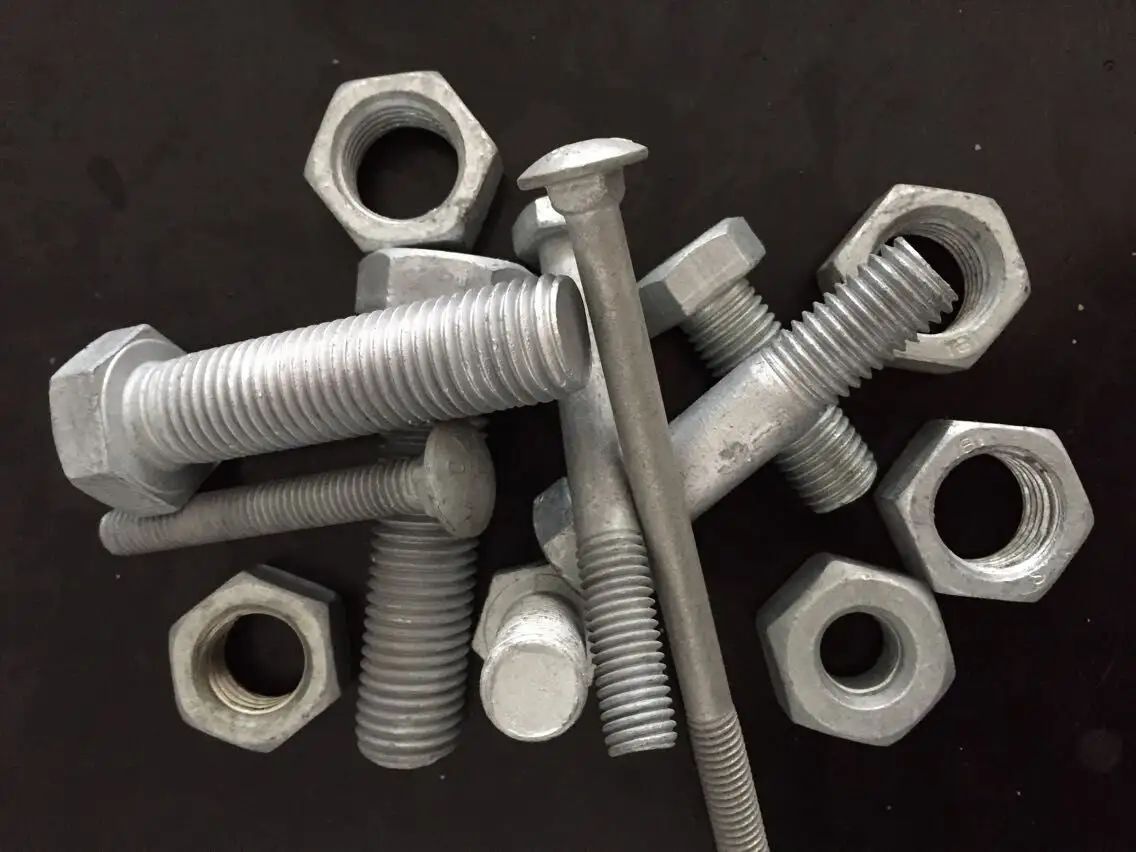
8. Infiltracja cynku
Infiltracja cynku jest stałą metalurgiczną powłoką dyfuzyjną cynku proszku. Jego jednolitość jest dobra, a jednolita warstwa można uzyskać zarówno w wątkach, jak i otworach w ciemno. Grubość poszycia wynosi 10-110 μm. A błąd można kontrolować na poziomie 10%. Jego wytrzymałość wiązania i działanie antykorozyjne z podłożem są najlepsze w powłokach cynkowych (takich jak elektrogalwanizacja, galwanizacja na gorąco i dacromet). Jego proces przetwarzania jest wolny od zanieczyszczeń i najbardziej przyjazny dla środowiska.
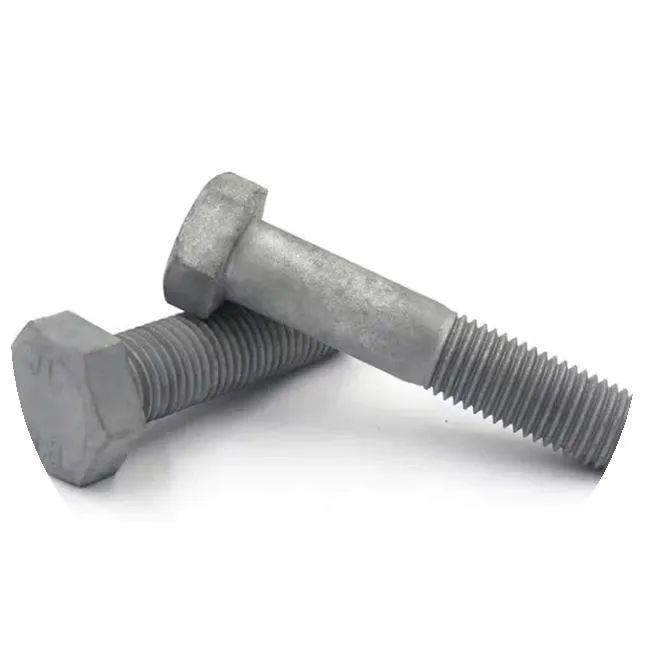
9. Dacromet
Nie ma problemu z kruchością wodoru, a wydajność spójności wstępnej obciążenia momentu obrotowego jest bardzo dobra. Bez rozważania problemów chromowych i środowiskowych Dacromet jest w rzeczywistości najbardziej odpowiednim dla mocników o wysokiej wytrzymałości o wysokich wymaganiach przeciwkorozowych.
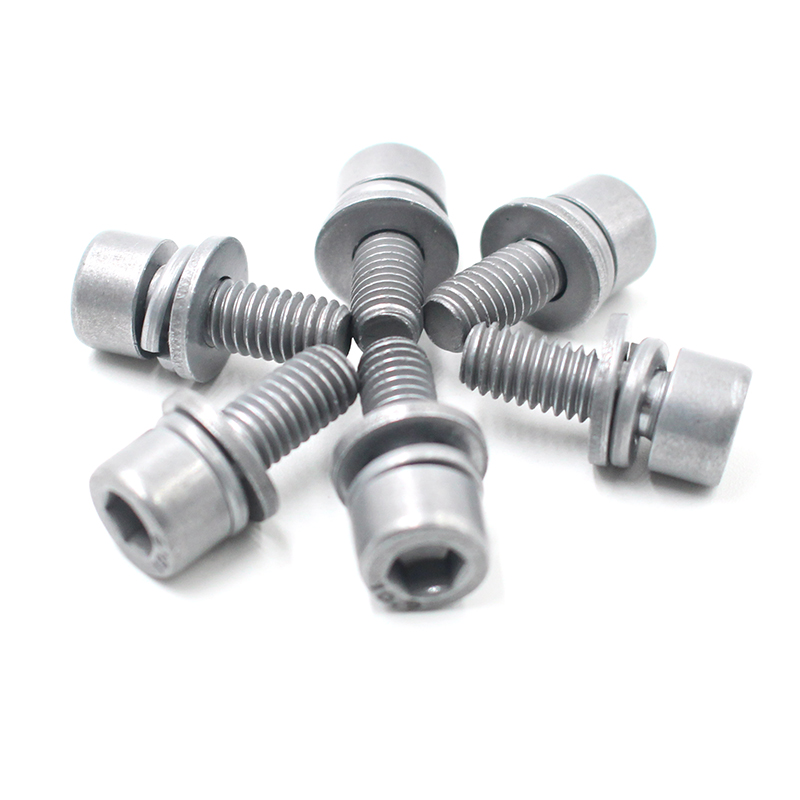
Czas postu: maja 19-2023